
HDP 1000 Brute Force Concept
Dense Phase Pressure System
|
The HDP 1000 Brute Force Concept Pressure Conveying System is a dense phase, high pressure, low to medium velocity, batch conveying system. It is generally used for conveying medium to high density, heat sensitive, semi-abrasive and/or abrasive materials over shorter distances. Examples include silica sand, plastic pellets, salt, quartz, whole grain, corn, oats and barley.
Typical conveying velocities are generally about 1000 feet per minute (5 m/sec) and the conveying pressure up to 60 PSIG (4 barg). A pressure vessel is used to feed material into the conveying line and the air supply, up to 100 PSIG (7 barg), is supplied from a high pressure air compressor.
|
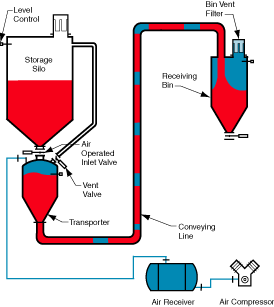
|

HDP 2000 Fluidizing Concept
Dense Phase Pressure System
|
The HDP 2000 Fluidizing Concept Pressure Conveying System is a dense phase, medium to high pressure, low to medium velocity, batch conveying system. It is generally used for conveying medium to high density, heat sensitive, semi-abrasive and/or abrasive materials under 100 mesh particle sizes. Examples include bentonite, cement, starch, silica flour, ball clay, kaolin clay, and alumina.
Typical conveying velocities are generally in the range of 1000 to 5000 feet per minute (5 m to 25 m/sec) and the conveying pressure up to 60 PSIG (4 barg). A fluidizing type pressure vessel is used to feed material into the conveying line and the air supply, up to 100 PSIG (7 barg), is supplied from a high pressure air compressor..
|
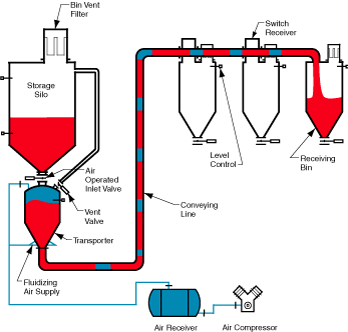
|

HDP 3000 Conventional Concept
Dense Phase Pressure System
|
The HDP 3000 Conventional Concept Pressure Conveying System is a dense phase, medium to high pressure, low to medium velocity batch type conveying system.
It is generally used for conveying high to medium density, heat sensitive, semi-abrasive and/or very abrasive, cohesive and/or very fragile materials in almost any particle size range. Examples include silica sand, glass batch, granulated sugar, powdered sugar, plastic pellets, bentonite, cement, starch, silica flour, ball clay, kaolin clay, zinc oxide and alumina.
Typical conveying velocities are generally in the range of 100 to 1000 feet per minute (0.5 m to 5 m/sec) and the conveying pressure up to 100 PSIG (7 barg) pressure.
This concept uses a non-fluidizing type pressure vessel to feed material into the conveying line at maximum density and utilizes DC-5 Air Saver technology to minimize and optimize the high pressure air which is supplied by a high pressure - up to 100 PSIG (7 barg) air compressor..
|
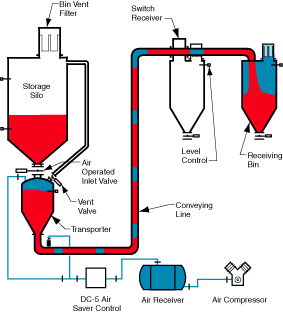
|

HDP 4000 Full Line Concept
Dense Phase Pressure System
|
The HDP 4000 Full Line Concept Pressure Conveying System is a dense phase, medium to high pressure, low to medium velocity, batch type conveying system. It is generally used for conveying medium to high density, heat sensitive, semi-abrasive and/or very abrasive, cohesive, and/or very fragile materials in almost any particle size range over long distances. Examples include silica sand, glass batch, granulated sugar, powdered sugar, finished breakfast cereal, coffee beans, plastic pellets, bentonite, cement, starch, silica flour, ball clay, kaolin clay, zinc oxide and alumina.
|
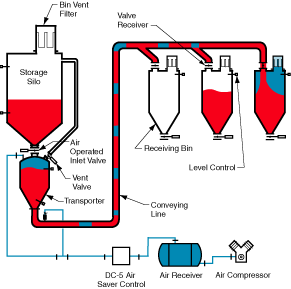
|

HDP 5000 Continuous Concept
Continuous Dense Phase Pressure System
|
The HDP 5000 Full Line Concept Continuous Pressure Conveying System is a dense phase, medium to high pressure, very low to medium velocity, continuous conveying system. It is generally used for conveying medium to high density, heat sensitive, semi-abrasive and/or very abrasive, cohesive, and/or very fragile materials in almost any particle size range over long distances. Examples include finished laundry detergent, silica sand, glass batch granulated sugar, powdered sugar, finished breakfast cereal, coffee beans, plastic pellets, bentonite, cement, starch, silica flour, ball clay, kaolin clay, zinc oxide, pelletized carbon black and alumina.
Typical conveying velocities are generally in the range of 100 to 1000 feet per minute (0.5 m to 5 m/sec) and the conveying pressure up to 100 PSIG (7 barg).
This concept uses two non-fluidizing type pressure vessels which operate alternately to feed material into the conveying line at maximum density. DC-5 Air Saver technology is used to minimize and optimize the high pressure air which is supplied by a high pressure - up to 100 PSIG (7 barg ) - air compressor.
|
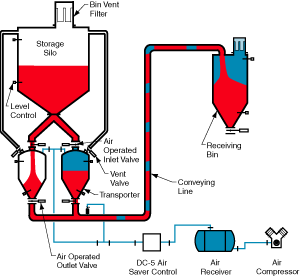
|

MDP 2000 Pressure Concept
Continuous Dense Phase Pressure System
|
The MDP 2000 Pressure Concept Conveying System is a dense phase, low pressure, medium velocity, continuous conveying system. It is used for conveying low density, heat sensitive, and non-abrasive materials over shorter distances where high pressure compressed air is available. Examples of materials that can be conveyed include plastic pellets, detergent powder, wheat, barley, corn, oats, limestone, coffee beans, granulated sugar, ball clay and boric acid.
Typical conveying line velocities are 2000 to 3000 feet per minute (10 m to 15 m/sec) and the conveying pressure is up to 15 PSIG (1 barg).
This concept utilizes a high density feeder to control the feed rate into the conveying line. The air is supplied by a high pressure - up to 100 PSIG (7 barg) - air compressor..
|
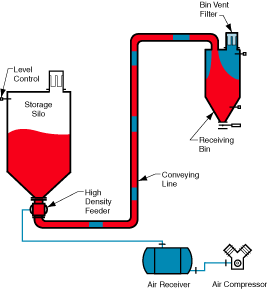
|

MDP 4000 Pressure Concept
Continuous Dense Phase Pressure System
|
The MDP 4000 Pressure Concept Conveying System is a dense phase, low pressure, low to medium velocity, continuous conveying system where compressed air is readily available. It is used for conveying low or medium density, heat sensitive, non-abrasive and/or friable materials over shorter distances. Examples of materials that can be conveyed include plastic pellets, finished detergent powder, limestone, coffee beans, granulated sugar, ball clay, boric acid, finished breakfast cereals and pelletized carbon black.
Typical conveying line velocities are 1000 to 2000 feet per minute (5 m to 10 m/sec) and conveying pressure is up to 15 PSIG (1 barg).
This concept utilizes a high density feeder to feed the material into the conveying line and DC-5 Air Saver technology to minimize and optimize the high pressure air which is supplied by a high pressure - up to 100 PSIG (7 barg) - air compressor.
|
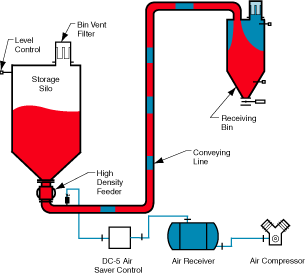
|

LDP 2000 Pressure Concept
Continuous Dilute Phase Pressure System
|
The LDP 2000 Pressure Concept Conveying System is a dilute phase, low pressure, high velocity, continuous conveying system. It is generally used for conveying low to medium density, and non-abrasive bulk solids where degradation of the conveyed material is not a concern. Examples of materials include flour, sugar, salt, grain, malt and plastic pellets.
Typical conveying velocities are generally in excess of 4000 feet per minute (20 m/sec) and conveying pressure is up to 15 PSIG (1 barg).
This concept utilizes a rotary airlock feeder to control the feed rate into the conveying line. A low pressure positive displacement blower is used for the air supply.
|
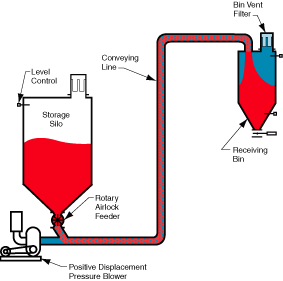
|

LDP 4000 Pressure Concept
Continuous Dilute Phase Pressure System
|
The LDP 4000 Pressure Concept Conveying System is a dilute phase, low pressure, medium velocity, continuous conveying system. It is generally used for conveying low to high density and/or non-abrasive materials where degradation of the conveyed material is somewhat of a concern. Examples include iron oxide, coffee beans, pinto beans, flour, fine chemicals, grain, malt, plastic pellets, sugar and salt.
Typical conveying velocities are generally about 2000 feet per minute (10 m/sec) and conveying pressure is up to 15 PSIG (1 barg).
This concept utilizes a rotary airlock feeder to control the feed rate to the conveying line. DC-5 Air Saver technology is used to minimize and optimize the low pressure supply air which is supplied by a low pressure positive displacement blower.
|
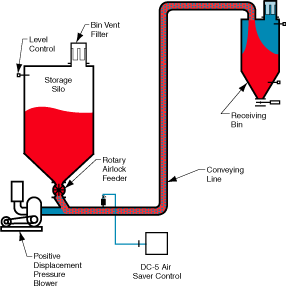
|

LDP 6000 Pressure Concept
Batch Dilute Phase Pressure System
|
The LDP 6000 Pressure Concept Conveying System is a dilute phase, low pressure, medium velocity batch conveying system. It is generally used for conveying low to high density, fluidizable, mildly abrasive materials that are not heat sensitive. Examples include sea coal, silica flour, bentonite, soda ash, cement, fly ash, alumina, and hydrated lime.
Typical conveying line velocities are generally about 2500 feet per minute (12.5 m/sec) and the conveying pressure is up to 15 PSIG (1 barg).
This concept uses a pressure vessel to feed the material into the conveying line while air is supplied by a low pressure positive displacement blower.
|
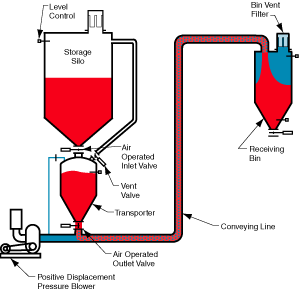
|

LDP 8000 Pressure Concept
Batch Medium Phase Pressure System
|
The LDP 8000 Pressure Concept Conveying System is a medium phase, low pressure, low to medium velocity, batch conveying system. It is generally used for conveying medium to high density, semi-abrasive, fluidizable materials which can be somewhat difficult to convey. Examples include coffee beans, powdered chocolate, ground limestone, calcium carbonate, alumina, iron oxide, cement and silica flour.
Typical conveying velocities are generally about 1500 feet per minute (7.5 m/sec) and the conveying pressure is up to 15 PSIG (1 barg).
This concept utilizes a pressure vessel to feed the material into the conveying line and DC-5 Air Saver technology to minimize and optimize the low pressure supply air which is supplied by a low pressure positive displacement blower.
|
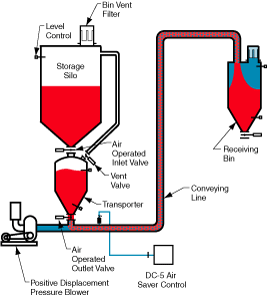
|

LDP 10,000 Full Line Pressure Concept
Continuous Medium Phase Pressure System
|
The LDP 10,000 Pressure Concept Conveying System is a medium phase, low pressure, low to medium velocity, continuous conveying system for longer distances. It is generally used to convey medium to high density, semi-abrasive, fluidizable materials which can be somewhat difficult to convey. Examples include coffee beans, powdered chocolate, ground limestone, calcium carbonate, alumina, iron oxide, cement and silica flour.
Typical conveying velocities are generally about 1500 feet per minute (7.5 m/sec) and the conveying pressure is up to 15 PSIG (1 barg).
This concept uses a pressure vessel to feed the material into the conveying line and DC-5 Air Saver technology to minimize and optimize the low pressure supply air which is supplied by a low pressure positive displacement blower.
|
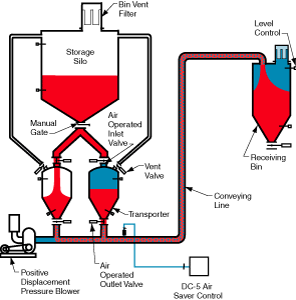
|

LDV 2000 Vacuum Concept
Continuous Dilute Phase Vacuum System
|
The LDV 2000 Vacuum Concept Conveying System is a dilute phase, high velocity, low pressure, continuous vacuum conveying system for shorter distances. It is generally used to convey low to medium density and non-abrasive materials. Examples include flour, kaolin clay, plastic pellets, grain, malt, corn, starch and plastic resin.
Typical conveying velocities are generally in excess of 4000 feet per minute (20 m/sec) and vacuum conveying pressures of up to 15 inches (381 mm) of mercury (hg).
The material is fed into the conveying line on a continuous basis by vacuum which is supplied by a low pressure positive displacement blower. The system includes a vacuum pickup nozzle, vacuum conveying line, a vacuum filter receiver, a rotary airlock feeder and a positive displacement blower..
|
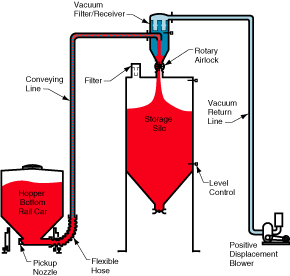
|

LDV 4000 Vacuum Concept
Continuous Dilute Phase Vacuum System
|
The LDV 4000 Vacuum Concept Conveying System is a dilute phase, medium to high velocity, low pressure, continuous vacuum conveying system for shorter distances. It is generally used to convey low to high density, non-abrasive and semi-abrasive materials. Examples include iron oxide, titanium dioxide, silica flour, cement, and limestone.
Typical conveying velocities are 1000 to 3000 feet per minute (5 m to 15 m/sec) and vacuum conveying pressures of up to 15 inches (381 mm) of Mercury (hg).
The material is fed into the conveying line on a continuous basis by vacuum. DC-5 Air Saver technology is used to minimize and optimize the low pressure supply air which is supplied by a low pressure positive displacement blower. The system includes a vacuum pickup nozzle, a vacuum filter receiver, a rotary airlock feeder and a positive displacement blower.
|
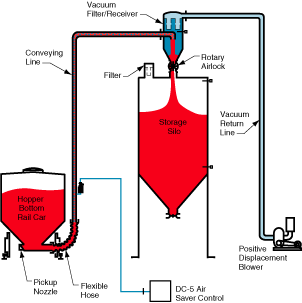
|

HDV 6000 Vacuum Concept
Continuous Dense Phase Vacuum System
|
The HDV 6000 Vacuum Concept Conveying System is a dense phase, medium velocity, high pressure, continuous vacuum conveying system.
It is generally used to convey low to high density, granular or pelletized, and semi abrasive materials. Examples include plastic pellets, granulated sugar, salt, coffee beans, pinto beans, and peanuts.
Typical conveying velocities are 300 to 1000 feet per minute (1.5 m to 5 m/sec) and vacuum conveying pressures of up to 29 inches (737 mm) of Mercury (hg).
The material is fed into the conveying line on a continuous basis by vacuum which is supplied by a high pressure vacuum pump. The system includes a vacuum pickup nozzle, a vacuum conveying line, a vacuum/filter receiver, a secondary filter and a vacuum pump. For continuous conveying applications, a gatelock hopper with an inlet and outlet valve is installed at the discharge of the vacuum receiver.
|
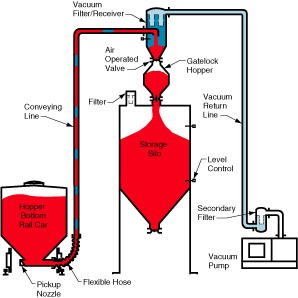
|

HDV 8000 Vacuum Concept
Continuous Dense Phase Vacuum System
|
The HDV 8000 Vacuum Concept Conveying System is a dense phase, low to medium velocity, high pressure, continuous vacuum conveying system. It is generally used to convey low to high density, friable, and abrasive materials and/or other materials where degradation or abrasion is a concern. Examples include plastic pellets, breakfast cereal, granulated sugar, salt, coffee beans, pinto beans, finished detergent, pelletized carbon black and silica sand.
Typical conveying velocities are 50 to 800 feet per minute (0.25 m to 4 m/sec) and vacuum conveying pressures of up to 29 inches (737 mm) of Mercury (hg).
The material is fed into the conveying line on a continuous basis by vacuum. DC-5 Air Saver technology is used to minimize and optimize the pressure supply air which is supplied by a high pressure vacuum pump. The system includes a vacuum pickup nozzle, a vacuum conveying line, DC-5 Air Saver controls, a vacuum filter receiver, a secondary filter and a vacuum pump. For continuous conveying applications, a gatelock hopper with an inlet and outlet valve is installed at the discharge of the vacuum receiver.
|
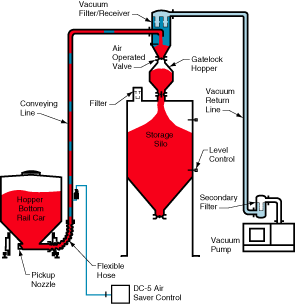
|
Copyright (c) 2007 Shin Shin International. All rights reserved. ssintl@chol.com |