The Lancaster K-Series continues the quality, sturdy construction, easy maintenance, and long life, which has been a Lancaster tradition for over 70 years.
All Lancaster Mixers are made of structurally rigid, fabricated steel construction. They are fabricated as a single unit and can be mounted on four corner pads under the heavy box beam framework.
Extensive efforts have been taken to eliminate material and dust leakage from the Lancaster Mixers. To avoid material leakage, the pan wall is a single piece, machine fabrication. The pan bottom is also a one piece construction, but with a central discharge opening. The opening is surrounded by a machined, tapered seal matching the discharge valve for a tight self-centering seal. The discharge valve assembly can be either air or hydraulically actuated.
|

These newly designed Lancaster AutoBrik Systems are hydraulically operated with PLC controls. These machines are designed for easy installation, simple operation, and low maintenance costs.
Lancaster Products produce 3 models of Lancaster Autobrik® Systems
The Lancaster AutoBrik Model 24H System is designed for the production of special shapes or limited production runs. The Model 24H is very versatile with fast and easy changing of mold sizes. The Model 24H can produce 4 standard brick equivalent/mold; however, the mold box area will accomodate molds up to 24" x 15-1/2" x 9-1/2" high.
The Lancaster AutoBrik Model 30H is an intermediate production system designed for moderate production rates. A mold can produce 6 standard brick.
The Lancaster AutoBrik Model 46H yields high production and is designed to operate in an automated system. (Production rates at 10 brick/mold are approximately 16,000 brick/hour.)
|

Material handling and batching machine
|
Lancaster Systems are designed and manufactured to control and automate your material storage, transporting and batching processes. A Lancaster System may be as simple as a day bin with a screw feeder and weigh hopper for the batching of a major ingredient, or a system may be as complete as a multi-story batching tower with bulk silo storage, pneumatic material conveying, individual batching of all materials, real time inventory, and a computer printout of every batch for complete traceability for quality control.
Kercher Industries, Inc. can also design and build systems to automate your production and finished product handling needs.
|

From the smallest laboratory 1/20th Hp model to a twin-shaft, heavy-duty pug mill using 150 Hp, Lancaster has a pug mill to meet your needs. Collapsible type wear resisting blades, replaceable wear resistant liners, steam jackets - whatever you requirements, we can handle them. Lancaster Pug Mills are individually designed to meet your specific application needs.
For design, manufacturing, service and parts, look for Lancaster Pug Mills.
|

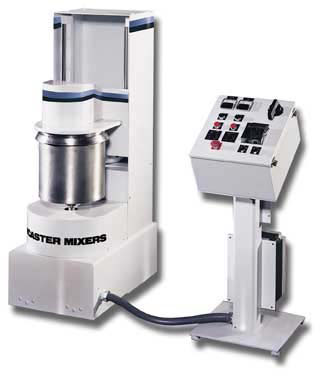
|
The Lancaster K-Lab Mixer was developed as a rugged mixer to economically meet the needs of most laboratory, prototype, or small production work. The K-Lab has the same counter-current mixing design as all Lancaster® Mixers with the clockwise rotating pan bringing material to the counter clockwise spinning rotor.
|

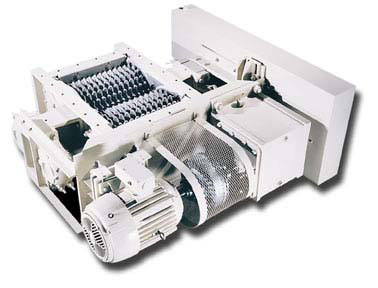
|
This Single Pass Material Crusher is designed to reduce materials of a given product size to a minimum size of 95 percent minus 3/4 inch, at rates up to 30 tons per hour. Provisions are made to permit particle size variation from 3/4 inch to 2 inches. Properly installed and operated, this crusher can reduce, in a single pass, material previously requring primary and secondary crushing. Lancaster® Roll Crushers are made for long life with a minimum of maintenance. The rolls turn toward each other, confining all crushing to the area where the teeth mesh. Both rolls are timed to rotate at the same speed to maintain a true crushing action with minimum fines.
|

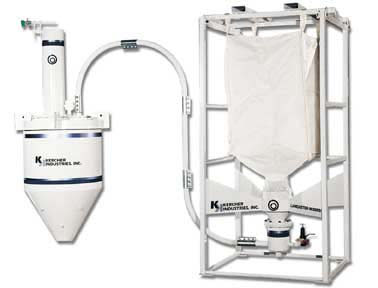
|
The Lancaster KT is a low-priced, unique, semi-dense phase pneumatic material transporter. The small unit has only one moving part, uses relatively little compressed plant air, has a simple control, uses standard 2" pipe and is capable of moving up to three tons of material per hour.
|

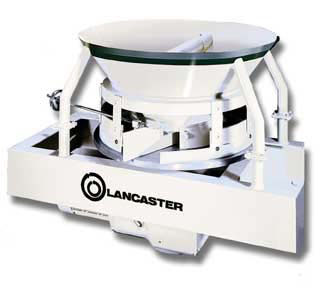
|
Lancaster® Rotary Table Feeders are used in industries which require the moving or feeding of powder or granular substances. Table feeders are particularly helpful in moving sticky or hard to feed materials. They are also very useful in converting an intermittent batch process into a continuous material feeding process.
|
±âŸ ÀÚ¼¼ÇÑ Á¦Ç° Á¤º¸´Â ¹®ÀÇÇØ Áֽʽÿä.
|
Copyright (c) 2007 Shin Shin International. All rights reserved. ssintl@chol.com |